Nordens högsta byggnad vilar stadigt i Göteborgsleran
Drygt 12 000 kubikmeter höghållfast betong har gått åt till de 58 grävpålar som ska bära skyskrapan Karlatornet i Göteborg. För att bemästra de utmanande markförhållandena krävdes nya smarta lösningar av teamet bakom rekordbyggnadens grundläggning.
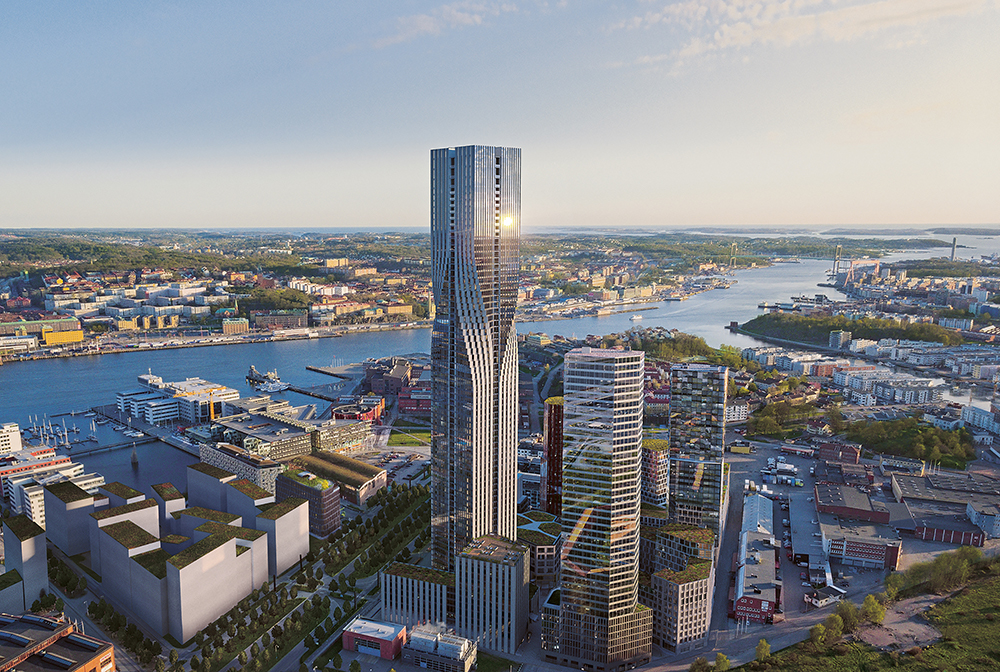
Illustration: Karlastaden Utveckling AB
När det står klart år 2021 ska Karlatornet vara 245 meter högt och innehålla 73 våningar för bostäder, kontor och hotell. Än så länge har byggnaden dock inte nått marknivå. Däremot sträcker den sig runt 70 meter under jordytan – genom ett 40–50 meter tjockt lager blålera, ytterligare cirka tio meter friktionsjord (grus, sten och block) och upp till sju meter in i den starka bohusgraniten där grunden förankras. Avståndet ner till berget, som dessutom lutar, var en utmaning. Grundläggningsmetoden som valdes kallas grävpålning och är ovanlig vid husbyggen i Sverige, men kan komma att användas betydligt mer i framtiden när allt fler höga hus byggs på instabil mark.
– Vi har jobbat med liknande teknik i Danmark tidigare, fast i mycket mindre dimensioner. Här i Göteborg mäter varje grävpåle två meter i diameter och ska enskilt kunna bära en last på omkring 4 500 ton. De är gjutna nerifrån och upp i ett foderrör av stål som vi borrat och tryckt ner i marken samtidigt som vi successivt schaktat ut lermassor ner till fast berg, säger Kim Bräuner Rasmussen, projektchef hos bygg- och anläggningsentreprenören Aarsleff, som utfört grundläggningsarbetet på uppdrag av entreprenadföretaget Serneke.

Illustration: Karlastaden Utveckling AB
Svårt borra i sättningskänsligt berg
Den sättningskänsliga Göteborgsleran är ett välkänt fenomen som alltid bjuder på utmaningar vid stora byggprojekt i staden, men även förankringen i det djupt liggande berget visade sig bli en svår nöt att knäcka.
– Berget i de här trakterna är både hårt och segt på ett väldigt speciellt sätt. När vi borrar med våra specialmaskiner får vi normalt bergsfraktioner på upp till 32 millimeter. Här var den typiska fraktionen bara noll till fyra millimeter. Det gjorde att vi fick borra med flera olika dimensioner för att frigöra spänningarna i berget innan vi började mejsla, förklarar Kim Bräuner Rasmussen.
Något som däremot gick enklare än förväntat var att få upp de långa foderrören ur marken allteftersom grävpålarna gjutits klart. Ett alternativ som diskuterades var att använda kvarsittande foderrör, men det hade blivit betydligt dyrare.
– Med hjälp av vibration såg vi till att inget rör stod still så länge att det riskerade att sugas fast i den omgivande leran. Det visade sig att även efter så lång tid som 13 dagar gick det utan problem att lossa röret och dra upp det, för att sedan återanvända det vid gjutning av nästa påle, säger Kim Bräuner Rasmussen.
12 000 kubikmeter höghållfast betong gick åt
Drygt ett år efter starten förra sommaren färdigställdes den sista grävpålen i början av september 2018. Omkring 30 betongsbilslass har krävts för varje påle, vilket innebär att det totalt gått åt över 12 000 kubikmeter höghållfast betong, tillverkad enligt ett recept särskilt framtaget för detta projekt.
– Vi började med labbförsök i juni 2017 och utgick efter den kravbild som gjutmetoden leder fram till. I och med att man börjar gjuta nerifrån botten av borrören så kommer den första betongen successivt pressas upp till ytan. Det innebär att den måste ha ett långt öppethållande och vara arbetsbar i 10–12 timmar, vilket är fyra gånger längre än normalt, säger Ingemar Löfgren, forsknings- och utvecklingschef hos betongleverantören Thomas Concrete Group C-lab® (Thomas Betong) och förklarar att speciella tillsatser och retarderande medel användes för att fördröja härdningsprocessen och erhålla de egenskaper som erfordrades.
Värmeutveckling viktig parameter
Ytterligare en utmaning var pålarnas djup, i snitt 60 meter. Det innebär att betongen i botten utsätts för väldigt höga tryck, vilket gör att överskottsvatten kan pressas ut (så kallad blödning) och skapa defekter i pålen. För att kontrollera detta användes en speciell provningsmetod där betongen utsätts för ett tryck och mängden blödvatten bestäms.
– Efter omfattande tester och provgjutningar med olika finmaterial och kalkstensfiller kom vi fram till en stabil sammansättning som inte är blödningsbenägen och samtidigt har goda gjutegenskaper för att omsluta armeringen samt uppfyllde kraven på tryckhållfasthet.
– Med så pass stora pålar, två meter i diameter, hade vi också värmeutvecklingen i betongen som en viktig parameter att ta hänsyn till. Risken är att man får väldigt höga temperaturer när betongen härdar, vilket i vissa fall kan ge problem. Därför använde vi Cementas anläggningscement ihop med en speciell slagg som vi tagit fram för massiva konstruktioner. Den bidrar till hållfastheten och hjälper också till att minska värmeutvecklingen, säger Ingemar Löfgren.
Injektering 30 har använts i efterhand
För att säkerställa resultatet används olika mätmetoder, exempelvis temperaturgivare som registrerar värmeutvecklingen i olika punkter och kan återskapa den färdiggjutna pålens geometri i en tredimensionell bild.
– Dessutom har varje påle ingjutna stålrör där vi har gått ner med borrstång och tagit ut kärnprover för att verifiera kvaliteten på både berg och betong. Via rören har vi också undersökt anläggningsytan mellan berg och betongpålen och vid behov injekterat dem med Injektering 30 för att fylla igen glapp som ibland uppstår mellan pålen och berget. I och med att vi genomfört så rigorösa provningar har vi bra kontroll på vad som hänt under gjutningen och hur pålarna ser ut, konstaterar David Salekärr, biträdande produktionschef vid Serneke Anläggning.
En intressant observation var att på grund av det höga trycket som betongen utsätts för så visade det sig att tryckhållfastheten vid botten av pålen var cirka 15 procent högre än vid toppen och vid botten var också densiteten fem procent högre. Detta beror på den komprimering som trycket orsakar.
Text: Susanna Lidström
FAKTA
Grunden lagd för ny stadsdel
Karlatornet kommer att bli Nordens högsta byggnad och är en del av Göteborgs planerade stadsdel Karlastaden, som ska bestå av åtta kvarter med bostäder, kontor, handel och service. Området utvecklas av Karlastaden Utveckling AB, ett bolag i Sernekekoncernen.
Ett nära samarbete mellan konstruktörer, entreprenörer och materialleverantörer har varit avgörande för att lyckas med Karlatornets djupgående grundläggning. Med samtliga 58 grävpålar på plats fortsätter nu arbetet med schaktning och spontning för att i början av 2019 kunna gjuta bottenplattan. Den ska placeras åtta meter under markytan och vara närmare fyra meter tjock.